Comprehensive Understanding of Graphite Gland Packing Technology
Graphite gland packing represents a significant advancement in sealing technology, offering unparalleled performance in demanding industrial applications. Unlike conventional packing materials, graphite-based gland packing combines exceptional thermal properties with remarkable chemical stability. The material's unique crystalline structure provides both lubricity and resilience, making it particularly valuable in applications where traditional packing would fail prematurely.
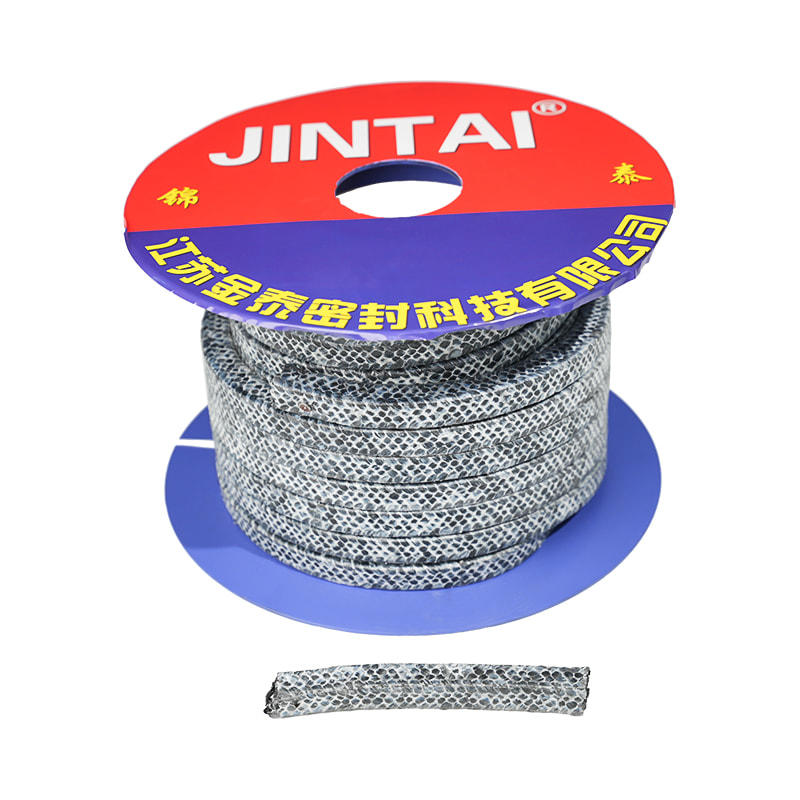
Fire Pump Valve Packing Glands Carbon Fiber Graphite Gland Packing
1.1 The Science Behind Graphite's Superior Performance
The exceptional properties of graphite packing stem from its molecular structure and manufacturing process:
- Crystalline alignment: The layered hexagonal structure allows for easy shear between layers, providing natural lubrication
- Thermal conductivity: With values ranging from 25-470 W/mK depending on grade, far surpassing organic materials
- Oxidation resistance: Special treatments can extend upper temperature limits by 100-150°C in oxidizing environments
Recent studies comparing graphite to alternative materials demonstrate clear advantages:
Property |
Expanded Graphite |
PTFE Composite |
Aramid Fiber |
Max Continuous Temp |
450-600°C |
260°C |
300°C |
Thermal Conductivity |
25-150 W/mK |
0.25 W/mK |
0.04 W/mK |
Compression Set |
10-15% |
25-40% |
15-25% |
pH Range |
0-14 |
0-14 |
4-11 |
1.2 Industrial Applications Where Graphite Excels
The unique combination of properties makes graphite packing ideal for numerous challenging applications:
- High-temperature pumps: Particularly in refinery and petrochemical services where temperatures exceed 300°C
- Chemical processing: Handling aggressive media including strong acids and alkalis
- Steam systems: Both saturated and superheated steam applications up to 100 bar
- Rotary equipment: Agitators, mixers, and other equipment with eccentric motion
Best practices for graphite valve stem packing installation: A Step-by-Step Master Guide
Proper installation methodology is crucial for achieving optimal performance from graphite valve stem packing. The process requires precision and attention to detail at every stage, from preparation to final adjustment.
2.1 Comprehensive Pre-Installation Preparation
Thorough preparation accounts for 40% of packing performance according to industry studies:
- Equipment inspection: Measure shaft/stem diameter at multiple points to check for wear (typically should not exceed 0.1mm variance)
- Surface finish verification: Ideal surface roughness (Ra) should be 0.4-0.8μm for optimal performance
- Stuffing box cleaning: Remove all old packing residues using specialized hooks and brushes, followed by solvent cleaning
- Packing measurement: Verify packing cross-section dimensions to within ±0.1mm of stuffing box clearance
2.2 Advanced Installation Techniques for Maximum Performance
The installation process requires methodical execution:
- Pre-forming rings: Wrap packing around properly sized mandrel to pre-form before installation
- Joint orientation: Stagger joints by exactly 90° for even-numbered layers or 120° for three-layer sets
- Compression sequence: Apply initial compression at 50% of final value, then operate equipment before final tightening
- Break-in procedure: Gradually increase pressure/temperature over 24-48 hours for optimal seating
High temperature graphite packing for steam applications: Engineering Considerations
Steam systems present unique challenges that demand specialized high temperature graphite packing for steam applications. Understanding these requirements is essential for reliable long-term performance.
3.1 Thermal Dynamics and Their Impact on Performance
Graphite packing behaves differently under steam conditions compared to ambient temperature:
- Thermal expansion coefficients: Axial expansion of 0.5-1.2mm/m at 400°C requires proper gland adjustment
- Heat transfer characteristics: Graphite's high conductivity (up to 150 W/mK) helps dissipate frictional heat
- Steam quenching effects: Rapid cooling cycles can cause micro-fracturing in inferior quality graphite
3.2 Pressure-Velocity (PV) Considerations in Steam Service
The relationship between pressure and velocity critically affects packing life:
Service Condition |
PV Limit (MPa·m/s) |
Expected Life |
Low Pressure Steam (<10 bar) |
2.5-3.0 |
3-5 years |
Medium Pressure Steam (10-40 bar) |
1.8-2.5 |
2-3 years |
High Pressure Steam (>40 bar) |
1.2-1.8 |
1-2 years |
Graphite packing leakage prevention techniques for Mission-Critical Systems
Implementing robust graphite packing leakage prevention techniques requires understanding both fundamental principles and advanced methodologies.
4.1 The Leakage Control Pyramid
Effective leakage prevention operates on multiple levels:
- Primary seals: Proper packing selection and installation
- Secondary controls: Lantern rings and injection systems
- Tertiary measures: Collection systems and environmental controls
4.2 Advanced Leakage Management Systems
Modern plants employ sophisticated techniques to minimize leakage:
- Laser alignment systems: Ensure <0.05mm runout for critical pumps
- Smart gland followers: Spring-loaded designs maintain constant compression
- Condition monitoring: Vibration analysis and thermal imaging predict failures
Comparing flexible graphite vs braided graphite packing: A Detailed Technical Analysis
The choice between flexible graphite vs braided graphite packing involves careful consideration of multiple technical factors.
5.1 Structural and Performance Characteristics
Fundamental differences between the two types:
Characteristic |
Flexible Graphite |
Braided Graphite |
Density Range |
1.1-1.3 g/cm³ |
1.0-1.2 g/cm³ |
Tensile Strength |
4-8 MPa |
10-15 MPa |
Compressibility |
30-40% |
25-35% |
Recovery Rate |
15-25% |
10-20% |
5.2 Application-Specific Selection Matrix
Decision factors for various operating conditions:
- High temperature static seals: Flexible graphite preferred for superior creep resistance
- Dynamic applications with vibration: Braided construction better handles mechanical stress
- Chemical exposure: Flexible graphite offers purer graphite content
Advanced Maintenance Strategies for Graphite Gland Packing Systems
Proactive maintenance extends service life and reduces total cost of ownership for graphite packing installations.
6.1 Predictive Maintenance Techniques
Modern approaches to packing maintenance:
- Thermographic monitoring: Track temperature profiles to detect abnormal friction
- Acoustic emission testing: Identifies microscopic leaks before they become visible
- Performance trending: Log leakage rates vs operating hours to predict end-of-life
6.2 Troubleshooting Flowcharts for Common Issues
Systematic approach to problem resolution:
- Excessive leakage: Check compression → inspect shaft → verify alignment
- Rapid wear: Review PV values → check lubrication → examine surface finish
- High friction: Verify break-in procedure → check for over-compression